Bethel Teferra, Senior Consultant at Ramboll, illustrates how a
modular, sustainable high-rise tower that evolves with a city's needs
could be a future reality and include engineered timber as key
component.
Modular houses may have been around for a while,
but modular high-rise with flexibility in function is a relatively new
concept. Imagine a high-rise building made up of modular units that can
be slotted in-and-out, with spaces for living, working and playing – a
building whose functions evolve according to a city's needs, built with
sturdy and sustainable materials and a building that's adaptable,
practical and eco-friendly.
Created by Haptic Architects and
engineering firm Ramboll, the 'Regenerative High-Rise' blends exactly
this flexibility and functionality and aims to redefine conventional
uses and lifespans of high-rise buildings in cities worldwide.
Constructed from a hybrid timber mix, the high-rise shows how tall
buildings can be both versatile and green at a time when climate change
is a pressing concern and requires a drastic rethink of the built
environment.
So how does this modular structure work? What are
the various uses for this type of building – and perhaps most
importantly, how can it be made more accessible?
The high-rise
structure aims to find the optimum between two key constraints:
flexibility in function and sustainability credentials via the use of
timber and other similar offsite production structural elements. To
equally satisfy the two constraints is a true balancing act as the
requirement for large spacious layouts imposes the need for higher
capacity structural elements, whereas sustainability is driven by
minimalism. Consequently, the highly loaded tower columns supporting
large spans with critical load-path are proposed in recycled steel, sand
timber-composite and modular options for frames defined within
three-storey 'villages'.
The core-wall (framing the lift shaft)
gives the high-rise structural lateral stability, using the Lateral
Force Resisting System (LFRS) via a precast and steel-brace solution
that provides sufficient lateral-stiffness against building sway,
enabling the building to resist environmental loads arising from wind
and seismic activity. Being an offsite manufactured solution, the
precast central-core provide sufficient stiffness and sustainable
solution, given its durability and low-carbon footprint.
Overall, the vertical elements including LFRS consist of a 20-40-40 timber-steel-precast ratio.
The
floor divide has a 'hard floor/soft floor' concept. The hard floors at
every third level work as a diaphragm mechanism to transfer lateral load
to LFRS in the overall structural system. These transfer-floors are
proposed to have the flexibility to support the construction of up to
three-storey 'villages' which consist of 'soft-floors' and other modular
plug-and-play frames. Hence, for the diaphragm horizontal elements,
cross laminated timber (CLT) floor construction with recycled steel
beams is proposed. The steel beams are used to reinforce the CLT
overall, to compose a robust floor-system that resists the above modular
three-storey floor occupancy loading as well as assist to meet its
serviceability limits. The horizontal elements have a timber-steel
proportion of 80-20. This timber-composite mix benefits the high-rise
with not only its low carbon footprint, but also imbues it with a warm
aesthetic.
The flexibility of the 'hard floor/soft floor'
concept is a highlight of the 'Regenerative High-Rise'. The innovative
structural and MEP design aims to serve multi-purpose occupancy
including hotel, residential, office, retail and entertainment, but the
high-rise's flexibility in design means it could also extend beyond
these functionalities too, if needed. For example, such buildings could
be used to cater to unexpected demands for flexible space as we've seen
during the recent COVID-19 crisis, which at its peak brought about a
sudden large need for extra hospital rooms, medical treatment centres,
testing facilities and quarantine spaces. In such cases, buildings with
flexible functionality would be best suited to meet great societal
needs, whilst also having a positive impact on the need for sustainable
and economical building solutions.
The project utilises offsite
construction and is inspired by Scandinavian prefabricated housing.
While prefab homes have existed for some time, modular towers are a new
and innovative concept, and the global construction market may be slow
to adopt new technologies compared to fast-moving industries like
information technology, automation, financial markets.
Construction
markets vary from region to region, depending on factors such as
economy, resources and natural environment. Contractors, engineers and
architects' familiarity in the design and delivery of offsite
construction solutions, as well as familiarity of skilled labour can be
key aspects to widespread adoption of offsite methods. While
professional institutions endeavour in continual education of engineers
and architects and stimulate wider discussion on latest innovations,
another idea to drive offsite to wider market can be that companies
specialising in these technologies could actively seek opportunities to
enter emerging market economies. Likewise, innovative and adoptable
holistic-building design solutions that are aspiring such as advanced
modular construction solutions contribute to the advancement of the
field – like the regenerative high-rise.
www.uk.ramboll.com
www.hapticarchitects.com
Regenerative High-Rise
5th September, 2022
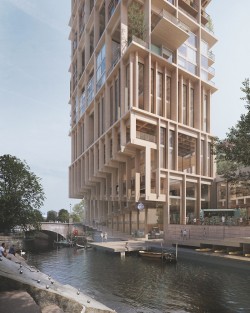